Roll Compactor Machine Working Process
The roll compactor is an essential tool, especially in the pharmaceutical industry. They cannot do without this machinery as they are apt for manufacturing tablets and capsules. This machine helps in the agglomeration (collection) of powder with all the necessary ingredients that are essential for the formation of the uniform size of granules. During the process, a specific amount of force is applied for the quality result. This method is called ‘dry granulation’. It enhances the material density and flow properties, making them suitable for various applications apart from the medical industry. It produces a thick sheet of durability and enhances the density of the produce by pressing it between the two rollers. Now you must be thinking how does the roll compactor machine function? For starters, the raw material is fed into the machinery for a consistent and high-mass flow rate of the raw- materials into the system.
How Does the Roll Compactor Machine Operate?
Let’s take a deep dive into the operation process of the roll compactor.
- Material Feeding:
The very first step is the material feeding into the roll compactor. The auger system facilitates this process to ensure a consistent flow rate of the raw- materials into the roller system. The machinery often consists of a vent that allows air to escape, which allows uniform material flow and compaction. Some of the advanced machinery also have screw-feeding mechanisms that will ensure a smooth material flow and eliminate the trapped air.
- Roller Compaction:
It is the central part of the roller compactor which enables uniform compression of the granules. The pressure applied by the rollers during the process is intense, which is facilitated by the machine’s hydraulic system. The rollers of the machinery are smooth and of specific diameter and width which also efficient and precise operations.
- Powder Compaction:
The material from the feeder system is compacted into flakes, ribbons, and sheets in the gap between the two pressure rollers.
- Granulation and Discharge:
After the above-mentioned process which results in ribbons and flakes, it needs further processing to achieve the desired size. Some of the key aspects of this stage are:
- Sieving: In this process, the compacted material is sieved to produce granules of appropriate sizes which are transferred to discharge the unit.
- Collection & Packing: After manufacturing the granules of the desired kind, they are collected and packed securely for further processing.
- Real-Time Monitoring:
Some of the high-quality compressing machines have real-time monitoring features like near-infrared spectroscopy (NIR) which helps in figuring out the changes that occur during the compression process. The NIR spectroscopy can evaluate the changes in the density and also detect the spectral changes during the process.
Final Words…
By understanding each stage and the parameter, the manufacturers can achieve the desired output. Precision is of utmost importance when it comes to the pharmaceutical industry and the roll compactor is here to just serve the purpose. If you too want to create a uniform and top-quality roll compactor like one from the brand ‘Riddhi Pharma Machinery Ltd’. They produce and supply products as per the needs of the clients. The innovative technology enables the manufacturing of equal grades of granules. You too much upgrade your operations by investing in the machinery for dust-free processing and increased bulk-density production.
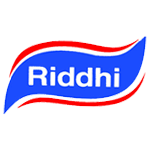
Riddhi Pharma Machinery Ltd.
Riddhi Pharma Machinery Ltd. has expertise in manufacturing pharmaceutical machinery. We have 28 years of experience in providing high-quality machinery solutions.